Cutting Tool Tribometer Overview
Main Features:
- Multiple test setups on same platform
- Real component testing and quick screening
- Several in-line sensors for advanced analysis
- In-line 3D profilometer to look at surface finish
Why Study? Machining is shaping materials into useful forms by removing the material. The cutting tool contacts with the work piece and either the tool, the work piece, or both while in motion. Cutting tool wear, final surface finish, cutting rate, metalworking fluids, additives, emulsifiers effect reliability and cost-effectiveness of the entire process. Study tribology and mechanical properties to improve machining and cutting tool process.
Rtec Cutting Tool Tribology solution comes with various test modules that mounts on the same platform. The test setups allows characterization of cutting inserts, tools, taps, drill bits, fluids, materials, coatings, process parameters, and many more. For a quick screen of the entire process or for research and development, we use this setup.
Need help or have a question?
Learn More About The MFT-5000 Platform
The MFT-5000 Tribometer
Learn more about the versatile MFT-5000 tribometer that provides friction, wear, and surface properties of various materials and coatings under a multitude of fluids, environments, and testing conditions.
Watch Cutting Tool Testing in Action
Test Setups On Same Tester
Simulate and improve the cutting tool process in a lab scale setup. Same real-life process parameters and finished component mounting generates useful data at a rapid pace. Interchangeable modules on same platform MFT-5000 presents a comprehensive cost effective solution.
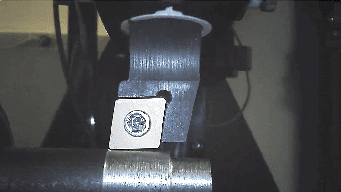
Cutting Tool Simulation
The cutting tool tribology module block on ring allows rotation of the shaft and while simultaneously moving it in Y direction. This provides simulation of a real machining operation. In-line torque measurement, controlled fluid flow rate, and temperature sensors. Integrated 3D profilometer measures surface finish and roughness of the cut surface.
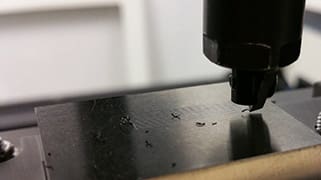
Scratch Adhesion and Hardness
The scratch and indentation module measures coating adhesion, hardness, scratch resistance, and more. Integrated 3D profilometer creates high resolution surface images to study surface damage.
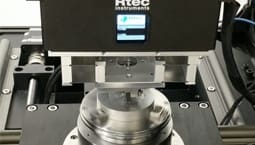
Spiral Wear Test
The cutting tool tribometer module rotary drive rotates the sample while simultaneously moving in Y direction to create spiral wear marks. This allows the cutting tool to see a fresh sample surface all the time. In-line friction, wear, controlled fluid flow rate, and temperature sensors. Integrated 3D profilometer measures surface finish and roughness of the cut surface.
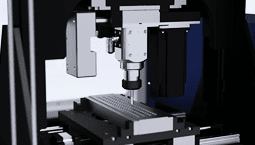
Tapping, Drilling, Cutting
The tribometer tapping torque module taps, drills, and cuts samples. Simultaneous upper rotation and lower XY stage allows simulation of real cnc operations. A wide range of taps can mount on the module. In-line torque, acoustic emission, controlled fluid flow rate, and temperature sensors.
Solution To
Our cutting tool tribology modules are used extensively across a wide range of industries:
-
Cutting Tools
-
Hard Coatings
-
Lubricants, Additives
-
Metal Working Fluids
The MFT-5000 Has More To Offer
Take a closer look at the Multi Function Tribometer.
Want to learn more?
Get in touch, and request a demo.
recommended
Information
© Copyright 2021 Rtec-Instruments - All Rights Reserved