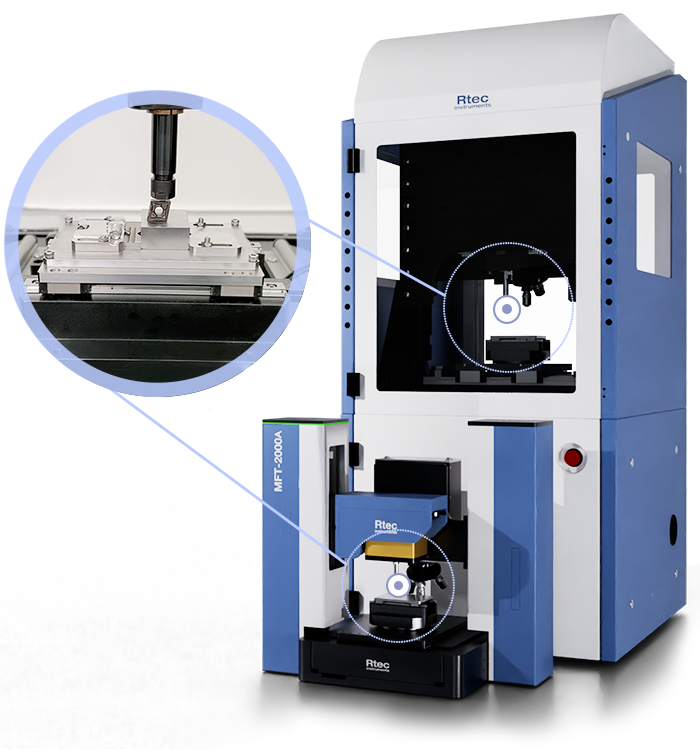
Detailed Module Information
- Piezo sensors for high frequency friction measurements
- Stroke 0.1 to 35 mm, up to 80 Hz frequency
- Dry and Liquid Tests
- Environmental Control Chambers (-50°C to 1200°C)
What is Linear Friction Tribometer? An upper sample – typically ball, pin or cylinder presses against the oscillating plate. Measure coefficient of friction (COF), friction force, wear rate, wear volume, temperature, and several other tribology parameters. The ball/pin-on-plate tribometer wear testing machine setup is ideal for characterizing tribology properties of alloys, ceramics, polymers, metals, coatings, and solid lubricants.
Rtec Solution—Our linear sliding wear tribometer module mounts on our tribometers. It works across a wide speed, load, temperature, and environmental range. Using various sensors it measures friction, wear, and adhesion of any reciprocating test setup with ease. The patented in-line 3D profilometer automatically measures topography change during the test. The module accommodates several application specific chambers, fixtures and test setups. It’s compliant to several ASTM, DIN, ISO standards including ASTM G133
Need help or have a question?
Learn More About The Platforms
The MFT Series Tribometers
Explore our MFT Series Tribometers for versatile surface and material testing.
One Platform. So Many Ways
The linear wear friction testing module accommodates several chambers and application specific setups. A wide load range of mN to 5000 N allows simulation of several linear tribology applications. Choice of module and test conditions depend on the final application.
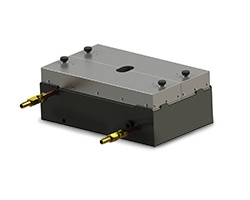
Cooling Chamber
Low temperature reciprocating tribology testing from -50°C
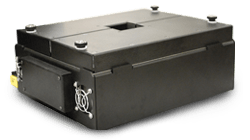
Heating Chamber
High temperature reciprocating tests room to 500 /1000/ 1200°C range.
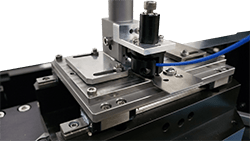
Wear with Capacitive Sensor
Fast reciprocating drive module allows for several test setups.
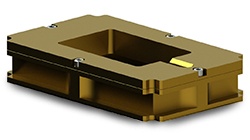
Liquid Container
Antisplash high speed liquid containers
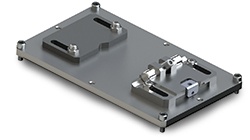
Sample Holder
Universal sample holder to mount samples with ease.
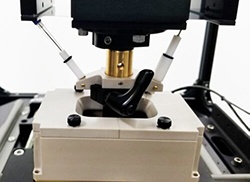
Tribocorrosion
Several application specific modules mount on the reciprocating drive.
Automatic In-line Imaging
Roughness, Wear, Volume vs. Time
Correlate friction, wear and topography easily.
The 3D In-line profilometer automatically measures the surface topography of the wear track. The module mounts on the XY stage that conveniently moves the sample between the test and image area.
The initial 3D image acquired using the profilometer accounts for machining marks, grain boundaries, orientation of the samples, and other localized features in contact surfaces. This information can be useful to explain the difference in friction, stick slip, and wear between specimens. This Figure shows an aluminum sample during a 2.5 hour ball-on-plate linear reciprocating test. The images were taken every 10 minutes.
Linear Wear Friction Testing Analysis
Ball On Plate Setup And Data
Setup
Materials are tested in pairs under nominally non-abrasive conditions. For the pin on plate tribology wear test, two specimens are required. One, a pin or ball that is positioned perpendicular to the other, usually a flat plate. The universal upper and lower sample holders are used to mount the samples.
Results
Figure shows the comparison of two different test samples tested at 200°C under similar conditions of load (200 N) and frequency against a 10 mm Cr6 ball. It is clear from the test that the Sample 2 has higher friction compared to sample 1.
Solution To
Due to its multiple configurations, the fast reciprocating tribometer module is used extensively across a wide range of industries:
-
Aerospace
-
Automotive
-
Bio-materials
-
Ceramics
-
Hard Coating
-
Lubricants
-
Metal
-
Pharmaceutical
-
Polymer
-
Hot, Cold Rolling
-
Medical devices
Need More Versatility?
Need Compact Tribology?
Learn about our benchtop Multi Function Tribometer, the MFT-2000.
Want to learn more?
Get in touch, and request a demo.
recommended
Information
© Copyright 2021 Rtec-Instruments - All Rights Reserved