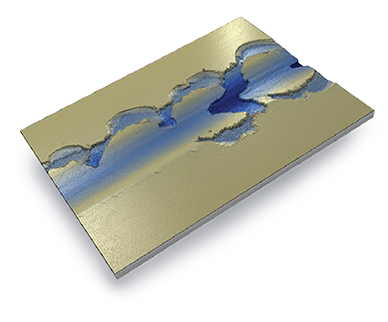
Product Page
The SMT-5000 performs scratch and indentation testing.
Application Notes
Put it in action. The SMT-5000’s versatility fulfills all scratch applications.
3D Scratch Adhesion Tester SMT-5000 Overview
Main Features
- Nano, Micro, and Macro Scratch ranges on one platform
- 3D surface panorama image of each scratch
- Patented in-line 3D imaging of scratch
- Normal and tangential forces are standard and measured atop the sample
- 3D Profiler and scratch data automatic correlation
Designed to quantify mechanical behaviors of bulk or coated surfaces from scratch. The SMT-5000 3D scratch tester measures scratch adhesion & cohesion, mar resistance, and hardness. Additionally, the scratch tester provides multi-pass wear at nano, micro, and macro scale.
The in-line integrated 3D profiler supplies unique analysis of failures with high resolution. Furthermore, the profilometer correlates the effect of roughness, features, and more.
Need help or have a question?
3D Scratch Tester Like No Other
Customizable To Fit Your Needs

Interchangeable Nano, Micro, Macro Scratch Measuring Modules
Down force from mN to 200 N (Higher force on MFT-5000 platform)

Patented In-line Profilometer
3D profiler automatically combines high resolution nm profiler data and scratch test data

Lower Interchangeable Motions
Scratch in linear, rotary or custom motion.
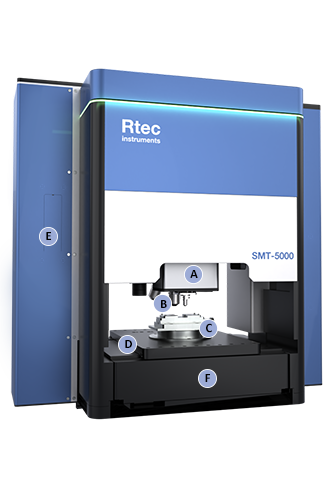

XY Stage
The high precision 210 mm XY stage moves test samples between testing and image positions. Besides this, the XY also aids in slow-speed reciprocating tests.

Upper Z Structure
High precision multiple Z drives with high resolution encoders moves between testing module and profilometer.

Platform
Open platform architecture for superior ease of use. Large sample testing volume, ability to mount and test any large dimension sample or full product.
Automatic Stitching Of In-line 3D Images
Scratch Data Visualization. Further analyze failure points and then relate to scratch data.
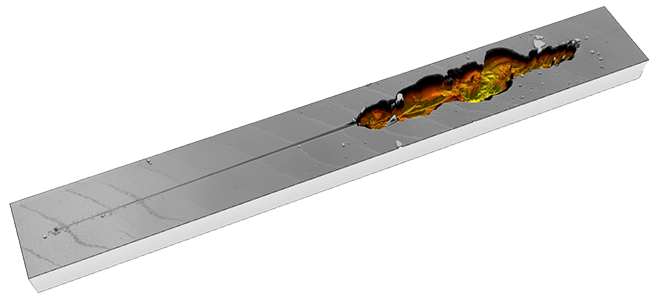
At the end of a scratch, the Universal 3D Scratch Tester SMT-5000 moves the sample under the optical microscope. By doing so, the profiler creates a full 3D panorama of the scratch. The combination measuring head and profilometer allow for measurement of scratch volume, depth, residual deformation, roughness, and volume wear. Furthermore, they provide a precise determination of points of failure with sub-nanometer resolution. Additionally, the turret of the profilometer allows up to 5 objectives. As a result, multiple simultaneous magnifications are possible.
Interchangeable Scratch Tester Heads On One Platform
Easy exchange of measuring heads accommodates nano scratch, micro scratch and macro scratch on the same platform.
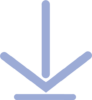
Nano Scratch Tester Head
UST-1
Max Down Force 1000 mN

Micro Scratch Tester Head
UST-40
Max Down Force 40 N
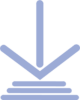
Macro Scratch Tester Head
UST-200
Max Down Force 200 N
Friction, Wear, and Coating Failures Data Correlation

Pre Test Image
First, the sample moves under the 3D profilometer to measure surface topography.

Scratch Test
Then, single or multiple scratches using predefined recipes are performed.

Post Test Image
The sample moves under the 3D profilometer to analyze the scratch area.

Report
Lastly, an automatic visualization for failures, adhesion, friction, cohesion, and roughness characterizations is reported. Residual depth, volume wear, and permanent deformation are easily calculated.
Patented Integrated Four Mode Profilometer
The profilometer is optimized to image scratch and indentation marks with high resolutions. Many automatic imaging modes image any sample surface. This includes transparent samples, glass, mirror, rough, smooth, steep slope, and much more with ease.

Dark Field Mode
Allows detection of cracks at the surface with notable contrast

White Light Interferometer Mode
Allows high resolution images of flat surfaces
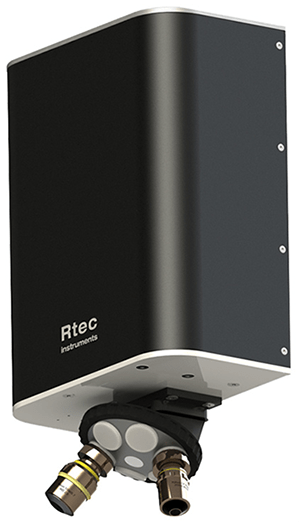

Spinning Disk Confocal Microscope Mode
Measures steep slopes, transparent, dark or rough surfaces

Bright Field Mode
2D profiles with high resolution and real colors
Load Profile and Custom Motions
Load Profiles: constant, linear increasing or decreasing, steps, or user’s defined load profiles. The applied normal force and resulting friction forces are measured using precise NIST traceable sensors with high thermal stability.
Various Motions: The automatic 210×150 mm XY stage can perform multiple scratch on single or multiple samples automatically. Scratch tests can be customize to achieve any motion profile –straight, curved, circle, zigzag, and more.
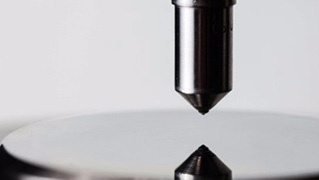
Scratch With Rockwell Tip
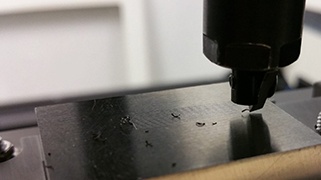
Scratch With Cutting Tool
Sensors and Chambers
Application specific solutions
Environmental chambers and a variety of sensors create numerous test variations that replicate real-life scenarios.
Electrical Contact Resistance
Identifies the coating failure point via the measure of the electrical resistance change during the scratch.
Acoustic Emission
Identifies brittle material failures by measuring the shock vibrations during the scratch.
Corrosion Setup
Allows scratch corrosion studies.
Environmental Chambers
Temperature, Humidity, and More.
Additional Sensors
Various sensors on coating scratch adhesion tester provides more information during the test.
Solution To
The SMT-5000 3D scratch tester is used extensively across a wide range of industries:
Aerospace
- Thermal Spray Coatings
- Turbine, engine, components
- Anti corrosive coatings
Automotive
- Marr ResistanceÂ
- Thermal Spray Coatings
- DLC
- Paints
Bio-materials
- Bio compatible coatings
- Medical devices
- Joints
- Valves, pumps
Ceramics
- Ceramic coatings
- Bulk materials
Hard Coating
- Cutting tools
- Thermal spray
- DLC
Metal
- Bulk Materials
- Coatings
- Textured surfaces
Optics and Glasses
- Lenses
- Touch screen
- Consumer goods
Pharmaceutical
- Coatings on tablet
Polymer
- Marr resistance
- Coating
- Bulk materials
Semicon
- Screens
- Thin coatings
- Protective coatings
- Consumer goods
What is a Scratch Tester?
The Rtec Instruments SMT-5000 Scratch Tester evaluates scratch adhesion, scratch hardness, and scratch resistance at a nano, micro, and macro scale. Read more below on how the SMT-5000 answers common scratch testing questions.

What tool is used for scratch testing
In order to perform a controlled scratch on the surface of a material, a scratch tester is used with a sharp tip. The tester applies and controls precisely the force (that can be either constant or changing) while sliding the sample at a constant velocity under a sharp tip. This combination of motion creates the scratch. Often, the tip used is made of diamond to allow scratch to be made on hard materials.

How is a scratch test performed?
A scratch is created by dragging a diamond tip of known geometry a top the surface of the sample of interest. As the tip is moved along the surface, the normal load applied to the tip is increased linearly, creating an increase in the severity of the contact. Following the scratch, images are taken of the entire scratch to analyze the different deformation and failures. The normal loads at which failures happen are called critical loads.

What is a scratch resistance?
Scratch resistance is the property of a material to resist the deformation created by the scratch test. This is often quantified using the permanent deformation left on the surface of the material.
Elastic Deformation
A less common analysis also considers the elastic deformation of the surface during the test. Those values can be found using the penetration of the tip into the material or using the comparison of 3D images pre and post-test.

How do you measure scratch adhesion?
In the case of a coating deposited atop a substrate, scratch testing allows the quantification of the adhesion between coating and substrate. By increasing the normal force on the tip to create failure of the coating, the user can distinguish typically the cohesive and adhesive failures of the coating / substrate system. The cohesive failure informs the strength of the coating, while the adhesive failure is the direct measure of the adhesion of the coating onto the substrate.
Need More Tribology Options?
Take a look at our Multi Function Tribometer, the MFT-5000.
Need Benchtop Tribology Options?
Want to learn more?
Get in touch, and request a demo.
recommended
Information
© Copyright 2021 Rtec-Instruments - All Rights Reserved