Product Page
The SMT-5000 performs scratch and indentation testing.
Application Notes
Put it in action. The SMT-5000’s versatility fulfills all scratch applications.
3D Microhardness Tester Overview
Main Features
- Widest Range mN to 40N on one head.
- Both indentation and scratch with the same head.
- Piezo and capacitive based for high precision.
- Patented image correlation between data and 3D images.
- In-line 3D Profiler to quantify cracks, pileups, defects, roughness, and position.
What is microindentation hardness testing?
Microindentation hardness testing (or microhardness testing) is a method to measure the hardness, modulus, and several other properties of a material on a microscopic scale.
Our Surface Mechanical Tester SMT-5000 combines piezo actuation and capacitive sensing technologies. The micro indentation head – IST brings the highest precision measurements, from nano to micron ranges. In addition, the SMT-5000 merges the ability to measure mechanical properties. Such as, hardness, modulus, scratch adhesion, film thickness, surface roughness, 3D imaging, and many others.
Besides the IST module, the SMT-5000 incorporates environmental modules (temperature, humidity, corrosion). All these capabilities of the SMT-5000 provide the use of microindentation for quality control. Or cater to demanding engineers and researchers in many fields.
Need help or have a question?
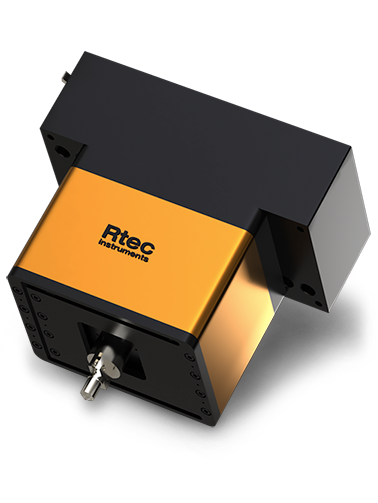
Instrumented
Microindentation Tester
Automatic load and displacement curves, Hardness (Traditional and instrumented), Elastic Modulus, Creep, and many more calculations.
- Microindentation + scratch test combination head from mN to 40 N
- Piezo controlled actuator for both Indentation and scratch mode
- Multi dimension capacitive force measurements
A Microhardness Tester Like No Other
The SMT-5000 is customizable and provides reliable microhardness and modulus analysis. Clear results every time.
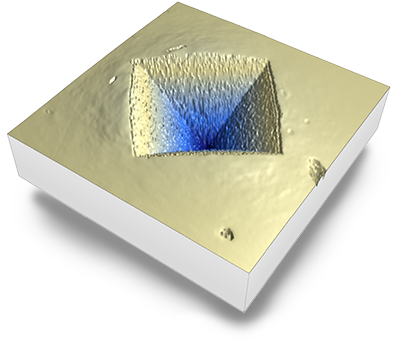
Automatic Microhardness Indentation 3D Image Using In-line Universal Profilometer
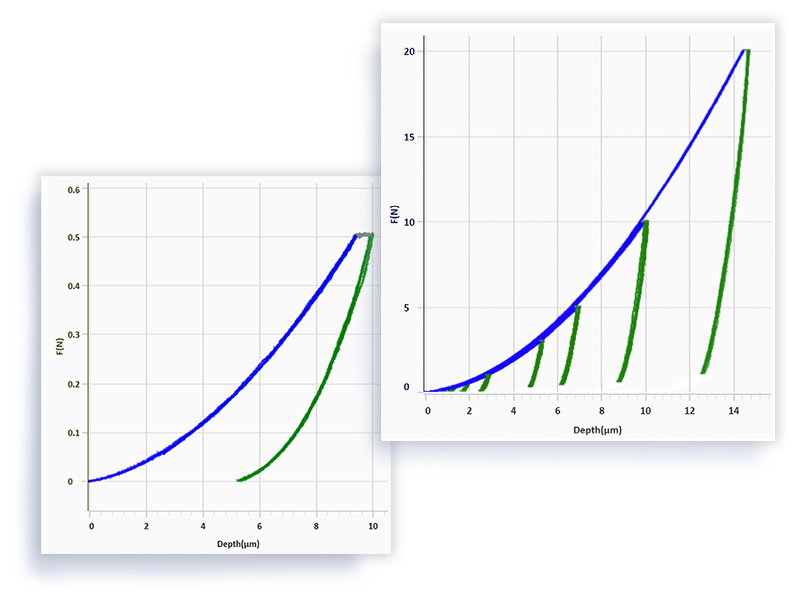
Indenters and Scratch Mode
Click of a button run (indent + 3D image + scratch)Â
Load Profiles: constant, linear, or user-defined applied load profiles. Measure the normal force and resulting friction forces using precise NIST traceable sensors.
Indenters: Berkovich, Balls, Cube Corner, Conical-Spherical, Knife, Knoop, Vickers, and more diamond indenters.
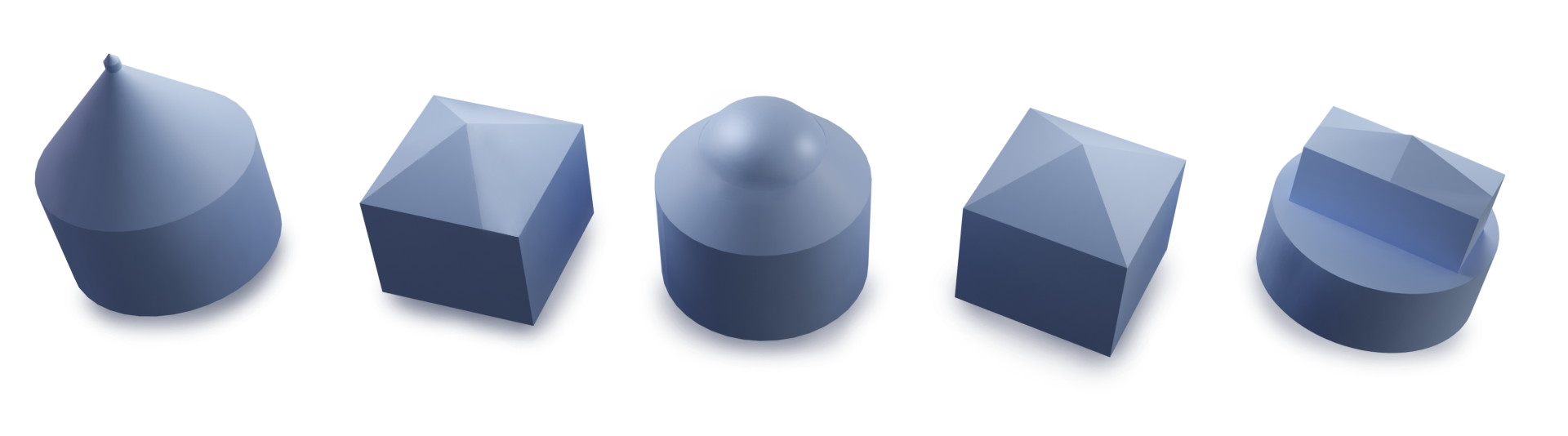
Scratch Testing
Characterize coating adhesion, mar resistance, hardness, and more.
The synchronization of data and 3D imaging ( Patent US 10,024,776 B2) is a unique and novel tool to study surface deformation and failures.
- Piezo actuator for precise down motion.
- The best friction force sensitivity on the market. One head provides normal and tangential force sensors.
- Multiple ranges from nano to macro on one platform. Easily interchangeable heads.
- Environmental control. (Temperature, humidity, corrosion, and many more).
- Measurement on a flat or curved surface.
- Click here for applications notesÂ
Sensors and Chambers
Application specific solutions
Environmental chambers and a variety of sensors create numerous microindentation and scratch test variations that replicate real-life scenarios.
Electrical Contact Resistance
Identifies the coating failure point via the measure of the electrical resistance change.
Acoustic Emission
Spot brittle material failures by measuring the shock vibrations.
Corrosion Setup
Study effect of corrosion material properties.
Environmental Chambers
Temperature, Humidity, and More.
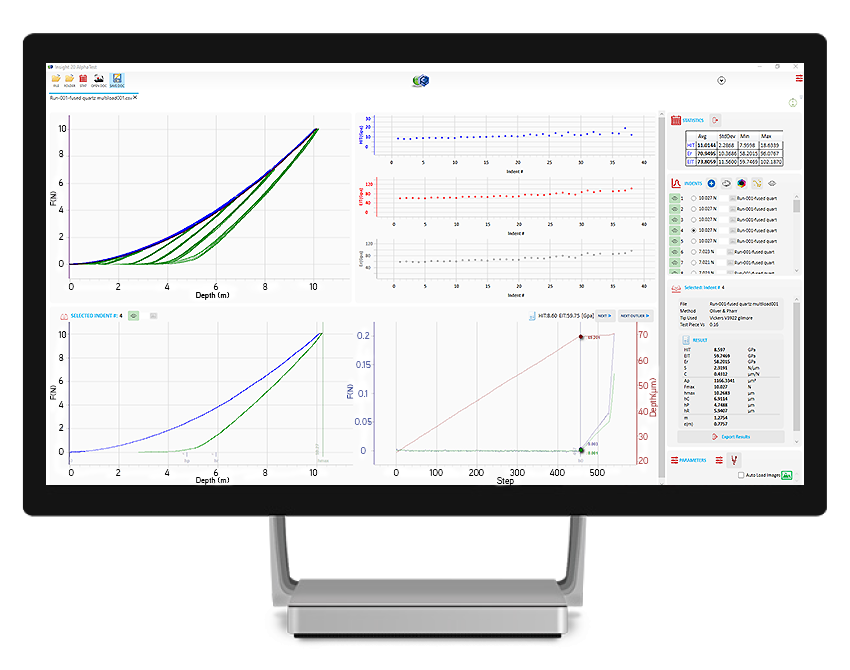
High Accuracy, easy to use, automatic reporting, and ASTM and ISO compliant. Simply load a recipe and click start. The software provides unequaled stability, precision, and insight.
The Microindenter Solution
Our SMT-5000 microhardness tester is used extensively across a wide range of industries:
Aerospace
- Thermal Spray Coatings
- Turbine, engine, components
- Anti corrosive coatings
Automotive
- Marr ResistanceÂ
- Thermal Spray Coatings
- DLC
- Paints
Bio-materials
- Bio compatible coatings
- Medical devices
- Joints
- Valves, pumps
Ceramics
- Ceramic coatings
- Bulk materials
Hard Coating
- Cutting tools
- Thermal spray
- DLC
Metal
- Bulk Materials
- Coatings
- Textured surfaces
Optics and Glasses
- Lenses
- Touch screen
- Consumer goods
Pharmaceutical
- Coatings on tablet
Polymer
- Marr resistance
- Coating
- Bulk materials
Semicon
- Screens
- Thin coatings
- Protective coatings
- Consumer goods
What is a Microindentation Tester?
The Rtec Instrument microindentation tester (or microhardness tester) measures hardness, elastic modulus, and many others at a microscopic scale. Read more below on how the SMT-5000 answers common microindentation testing questions.

What Is Instrumented Indentation testing?
Instrumented Indentation Testing (IIT) involves pressing an indenter of known geometry into a surface while controlling and measuring the force and displacement. The resulting load-displacement curves are used to calculate hardness and elastic modulus among other things.

How is hardness measured in indentation?
Hardness is defined as a contact pressure (Force by contact area).
Traditional hardness tests use the maximum force applied on the tip and the visual measurement of the size of the imprint left into the material (after removal of the force) to calculate Hardness values.
IIT also uses the maximum force applied on the tip, but calculates the true cross-sectional area of contact between the tip and the material at the point of maximum force

What is the difference between IIT and traditional hardness tests?
Traditional hardness tests provide only one characteristic: hardness. Furthermore, most hardness tests rely on the optical observation and measurement of an indent under a microscope. This often creates uncertainty and operator error due to the different magnifications available on the microscope.
Why IIT is Different
IIT brings additional information about the material. Such as the elastic modulus, that the conventional hardness could not measure. Additionally, the direct calculations of the area used for Hardness in IIT eliminate the possible errors introduced by users. It instead measures the imprint optically rather than traditional hardness tests. Finally, the use of much lower forces in IIT allows for the investigation of much smaller volumes of materials. This opens the ability to measure coatings independently from their substrate.

How is modulus measured using IIT?
Elastic modulus is the ability of a material to “bounce back” after applying stress. By its control and recording of force and displacement, IIT can provide the elastic modulus of the material tested by studying the unloading portion of the test. After the maximum force is applied to the material, the test’s unloading portion represents the material’s elastic response. A fitting of the unloading curve accompanied by using different models yields the value of the elastic modulus.
Want More Tribology Options?
Learn more about Multi Function Tribometer, the MFT-5000.
Need Precision Nanoindentation?
Want to learn more?
Get in touch, and request a demo.
recommended
Information
© Copyright 2021 Rtec-Instruments - All Rights Reserved