溶射コーティングのスクラッチ試験 はじめに
ご質問はございますか
問題のあるスクラッチ試験
スクラッチ試験の方法論
基板/溶射システムは、金属組織マウントに断面として取り付けられ、研磨されて基板とコーティングの間の界面が露出します。 一定の荷重スクラッチは、球状円錐形のダイヤモンドチップを界面に垂直にドラッグし、基板からコーティングに向かって移動することによって生成されます(図1)。 取付材に傷を付けて仕上げます。
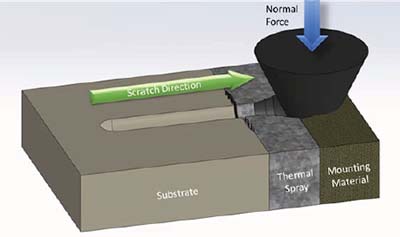
Figure 1: 断面スクラッチ試験の原理
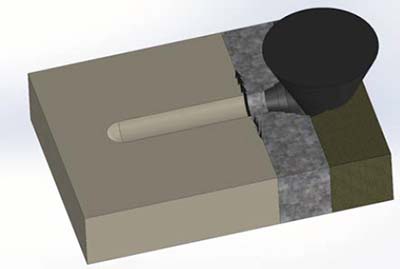
Figure 2: 断面スクラッチ試験の不良
- 溶射コーティング内部の亀裂と自由表面でのコーティングの円錐破壊によって示される凝集破壊
- 基材と溶射コーティングの界面に亀裂が発生した場合の接着不良。
スクラッチ試験条件
加重条件 | 一定加重 |
スクラッチ長 | 2 mm |
加重 | 20 & 30 N |
スクラッチ速度 | 4 mm/min |
スタイラス | Rockwell with Φ200 µm |
荷重ごとに3つのスクラッチ(図3)が各サンプルで実行され、サンプルごとに合計6つのスクラッチが実行されます。 一定の荷重値は十分な損傷と接着不良をテストする可能性を生み出すために選択されました。
溶射コーティング接着試験結果
金属組織マウントに取り付けられた4つの異なる溶射断面をテストして、コーティングの特性(凝集力と接着力)を調査しました。
コーティングにはさまざまな種類の不良が見られます。
接着不良
この場合、溶射と基板の界面に亀裂が発生しました。 この不良は溶射コーティングと基材の間に存在する接着の強さに直接関係しています。 亀裂は常に界面から発生し、界面に沿ってまたはコーティングの内部に伝播する可能性があります。
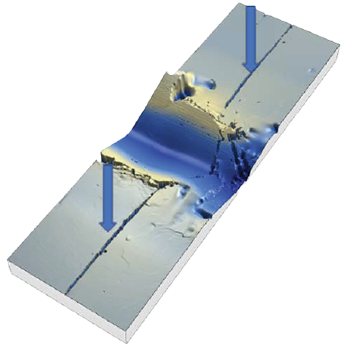
Figure 4:インターフェースでの接着不良
スクラッチ溝の両側の亀裂の長さを使用して、接着不良の重大度を定量化できます。 この失敗が観察された場合、テストのエネルギーの大部分がコーティング/基板の界面の失敗に費やされるため、他の結論を出すことはできません。
コーティングの凝集破壊
このタイプの故障は、スクラッチ溝の側面からコーティング自体に伝播するいくつかの亀裂によって特徴付けられます。 亀裂の起点と終点の両方が溶射コーティングにあります。
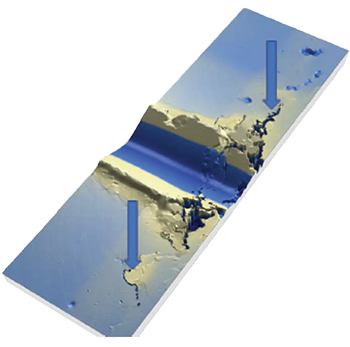
Figure 5: コーティングの凝集破壊
この不良はコーティング自体がその不良領域に含まれているため、コーティング自体の強度に直接関係しています。
自由表面での凝集破壊
最終的なタイプの不良は溶射コーティングの自由表面に見られ通常は円錐の形をしています。 この破損は、溶射コーティングの凝集力にも関係しますが、コーティング内部で発生する亀裂よりも高い凝集力を示します。 この不良は溶射がその自由表面に向かって失敗した結果です。
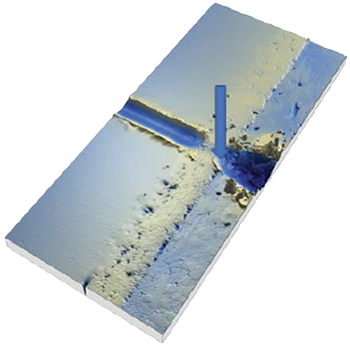
Figure 6: コーティングの自由表面での凝集破壊
自由表面の前に他の破損が観察されないことを前提として、この破損を示すサンプルは円錐破損の角度を測定することによってランク付けできます。
角度が小さいほど、溶射の凝集力が高くなります。
溶射サンプルの比較
Figure 7: TS1およびTS3の角度測定
溶射コーティングのスクラッチテスト結果の概要
この研究では、4つの溶射サンプルを実行しました。
接着から凝集までさまざまな不良を示しました。 すべてのサンプルの結果を表2にまとめています。
サンプル | Y/N | クラック長 (µm) |
---|---|---|
TS 1 | N | |
TS 2 | N | |
TS 3 | N | |
TS 4 | Y | 357 |
サンプル | Y/N | クラック長 (µm) |
---|---|---|
TS 1 | N | |
TS 2 | Y | 124 |
TS 3 | N | |
TS 4 |
サンプル | Y/N | fracture con 角度(°) |
---|---|---|
TS 1 | Y | 71.54 |
TS 2 | ||
TS 3 | Y | 58.24 |
TS 4 |
結論
参考文献
2 ISO 27307 – 2015 Thermal spraying — Evaluation of adhesion/cohesion of thermal sprayed ceramic coatings by transverse scratch testing
3 Lopez, Zambelli, Cohesion measurement of plasma sprayed ceramic coatings, Surface Modification Technologies (815-821), 1990
3Dスクラッチ試験機にはさらに多くの機能があります
用途の広いスクラッチテストが必要ですか
もっと知りたいですか?
ご質問など、お問い合わせください。
おすすめ機種
インフォメーション
© Copyright 2021 Rtec-Instruments - All Rights Reserved