ハードコーティング品質管理
はじめに
Figure 1: PVDコーティングの典型的な用途:インサートと切削工具
ご質問はございますか
テストの原則
「スクラッチテストは、コーティングされた表面の機械的完全性を評価するために設計されています。テスト方法は、一定または漸進的な垂直力の下で、テスト対象のコーティング-基板システムの表面全体にスタイラスを描画することにより、定義された形状のスタイラス(通常はロックウェルCジオメトリのダイヤモンド)でスクラッチを生成することで構成されます(Fig.2)。不良は、引っかき傷を直接顕微鏡で観察し、場合によってはアコースティックエミッションや摩擦力の測定を使用して検出されます。」
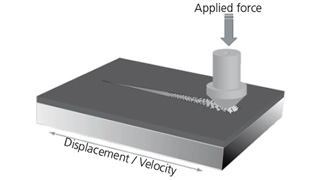
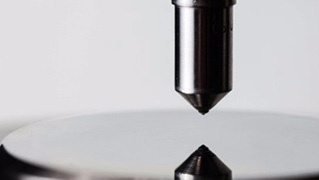
一定または荷重増加を使用したテストを検討できます。 荷重増加は単一のテストで臨界荷重、したがって、凝集および/または接着破壊が観察される臨界応力を決定することです。 Fig. 3に示すように、比較的迅速なテストにより、コーティングの接着が失敗する臨界荷重を測定できます。
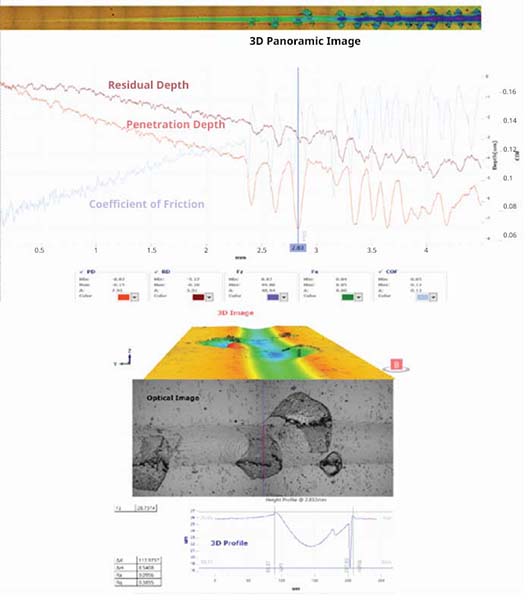
Figure 3. TiNコーティングのインライン3Dイメージングによるスクラッチ結果のデータ分析の原理
特性評価方法
凝集破壊(コーティング内部の剥離、通常はTiNコーティングで観察される)は、サンプルの機械的強度に関する興味深い見解を提供します(Fig. 4を参照)。
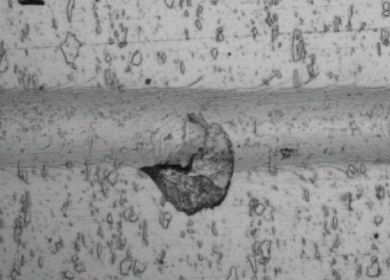
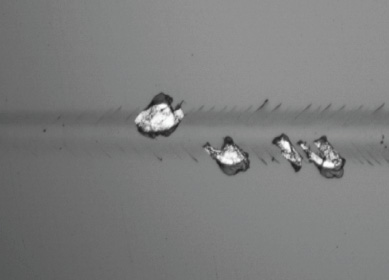
したがって、臨界垂直力Lcは、コーティング-基板システム(または多層コーティング-基板)の機械的完全性に関連しています。 システム内の機械的応力は、Fig. 5のように概略的に表すことができます。
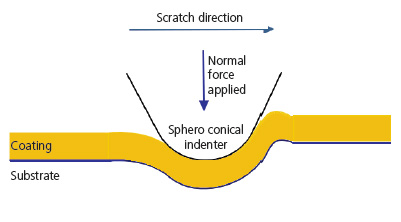
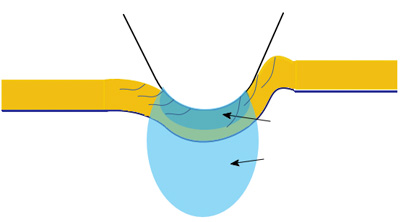
Lc1は一般に最初の亀裂の出現と見なされ、Lc2は最初の層間剥離または剥離と見なされ、Lc3は完全な層間剥離と見なされます。 Lc1、Lc2、およびLc3の例をFigure 6a-cに示します。
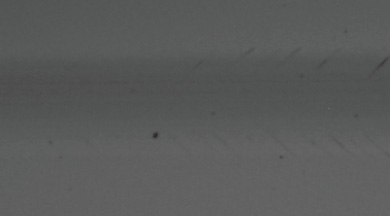
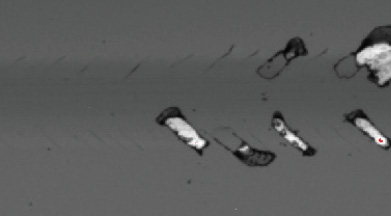
Figure 6b Lc2: First Delamination
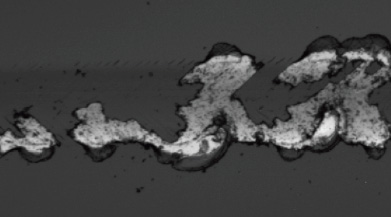
Figure 6c Lc3: 完全な層間剥離
臨界垂直力Lc(n)の決定は、臨界荷重の一般的に受け入れられている名前Lc(n)でもあり、最も解釈の対象となる試験の側面を表す可能性があります。課題は2つの側面にあるかもしれません
- 検出の難しさ:ハードコーティングの典型的な亀裂は、アコースティックエミッション(AE)センサーで検出できますが、光学的に観察するのは難しい場合があります。したがって、どの検出方法(顕微鏡、侵入深さ、AEまたは摩擦)も、この検出にとってより価値があります。
- 誤解:一部の障害モードは、さまざまなユーザーによって異なる方法で解釈される可能性があります。
しかし、品質管理では、これらは最初の調査で最初から簡単に取り除くことができます。特定のコーティング-基板システムでの破損モードは再現性が高くなります(つまり、TiNコーティングは典型的な凝集破損を示しますが、DLCコーティングは接着不良を示す傾向があります)。また、誤解を招くことなく、どのLc(n)が最も意味があるかを判断するのも簡単です。
ハードコーティングの品質管理におけるスクラッチテスト特定の側面
圧子先端の特性評価
テスト自体は、球状円錐圧子とコーティング表面の間の強力な機械的相互作用に対応しており、その結果は、局所的な接触面積のわずかな変動に大きく依存します。 したがって、チップの品質を定期的にチェックすることが非常に重要です。
Rtec-Instrumentsは、スクラッチ試験機に統合された共焦点顕微鏡を提案しています。これにより、高解像度の3D画像で圧子の先端を高速に制御できます。 先端の損傷や汚染は簡単に観察できます。 超音波浴および/または機械的研磨によるチップの定期的な洗浄は、スクラッチ試験のための効果的な一貫した接触領域を確保するのに役立ちます。 このプロセスは、スクラッチテストの制御手順で実装できます。
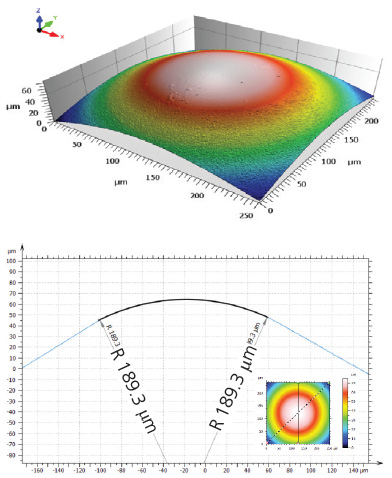
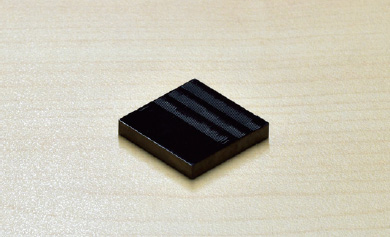
検証と校正
認定されたリファレンスサンプルには、機器とスクラッチ圧子チップの両方の検証を同時に提供するという大きな利点があります。圧子チップは、同様に検証される他の重要なパラメータの1つです。
形状と表面粗さ
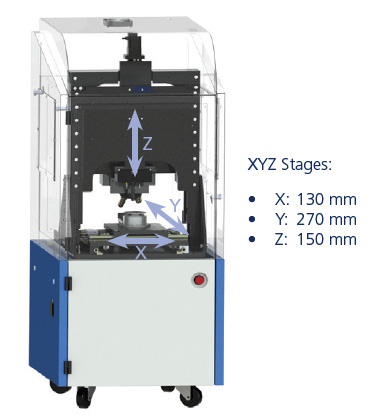
ハードコーティングの品質管理と複数のサンプルプログラミングの自動化
品質保証のスクラッチ試験モード
Progressive-Force Scratch Test
圧子が試験面を一定速度で横切ると、圧子によって加えられる垂直力は直線的に増加します。 力が増加するにつれて、圧子は徐々に層に浸透します。 侵入深さが増加すると、ダイヤモンドによって誘発される応力も増加します。 Rockwellの半径が200mmで、国際規格に準拠しているハードコーティング(2〜6 mm)の場合、100 N / minおよび10mm / minのパラメーター値をお勧めします。 故障に使用される臨界負荷が10N未満の場合は、より低い負荷率をお勧めします。 スクラッチ中、特定の力(亀裂、剥離、完全な層間剥離などの臨界荷重(Lc))に達すると、これが材料の破損を引き起こす力の値(圧力)になります。
Constant-Force Scratch Test
垂直抗力は、破損が発生するまで、試験片表面のさまざまな場所で一定の垂直力の下で実行される連続する引っかき傷の間で段階的に増加します。Progressive-Force Scratch Testで決定された臨界垂直力の5分の1を使用して、10 mm / minの圧子トラバース速度を使用して、増加する垂直力で一連のスクラッチが生成されます。より低い垂直抗力増分を使用する新しい一連のスクラッチを使用して、関心領域をより詳細に調査できます。一定の力は、最高の精度で破損の臨界荷重を決定すること、または表面の広い領域をスキャンすることによってサンプルの均一性を決定することです。一定の力を自動化された複数のテストで実行して(各テストシリーズで一定の力を増加させて)、最初の亀裂、最初の層間剥離、および完全な層間剥離の臨界荷重を統計的かつ最高の精度で取得できます。時間制限の実際的な理由から、Constant-Force Scratch Testは、Progressive-Force Scratch Testよりも産業用アプリケーションで使用されていません。Progressive-Force Scratch Testは、信頼性の高い十分なデータを提供しながらはるかに高速であるためです。
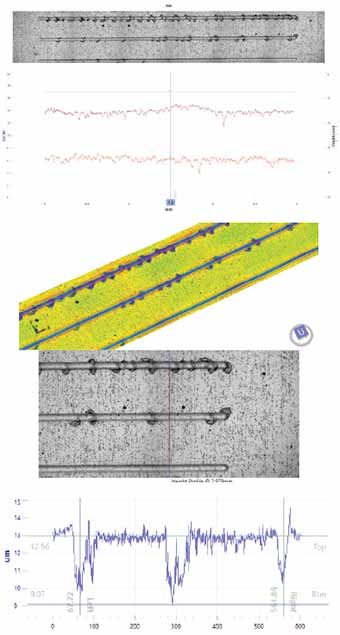
Multi-Pass Scratch Test またはトライボロジーテスト
Multi-Pass Scratch Test またはトライボロジーテスト試験片は、一定の亜臨界垂直力の下で、同じスクラッチトラック内で繰り返しスクラッチを受けます。 Progressive-Force Scratch Testで決定された垂直力の50%、圧子の移動速度10 mm / min、スクラッチ長3 mm以上を使用して、破損が発生するまでサンプルをテストします。 このモードは、実際の作業条件に近いが、トライボロジー試験と同等の低サイクル疲労タイプの接触を表します。 スクラッチテスターは、線形往復振動モードのトライボメータのように使用できます。
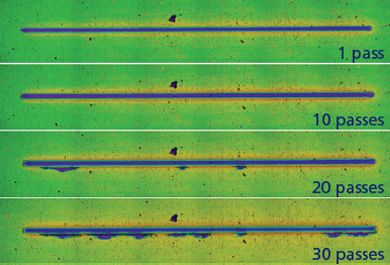
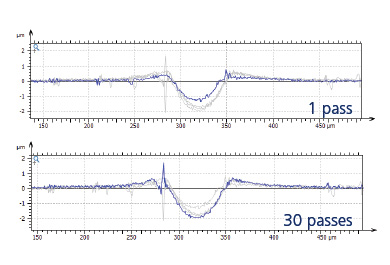
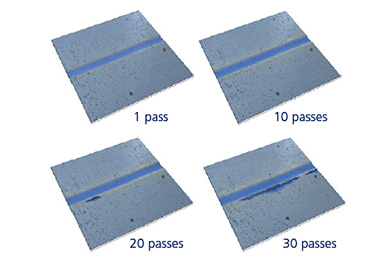
スクラッチテスト法による
品質管理の関心と結論
参考文献
定量的シングルポイントスクラッチ試験によるセラミックコーティングの接着強度と機械的破損モードの標準試験方法。
ISO 20502 (2005-reviewed and confirmed in 2019) Fine ceramics (advanced ceramics, advanced technical ceramics) – Determination of adhesion of ceramic coatings by scratch testing.
ファインセラミック(アドバンスドセラミック、アドバンスドテクニカルセラミック)-スクラッチテストによるセラミックコーティングの接着性の測定。
3Dスクラッチ試験機にはさらに多くの機能があります
用途の広いスクラッチテストが必要ですか
もっと知りたいですか?
ご質問など、お問い合わせください。
おすすめ機種
インフォメーション
© Copyright 2021 Rtec-Instruments - All Rights Reserved