Home > インデンテーション、スクラッチ試験機 > アプリケーション >
スクラッチ接着性とハードコーティングの凝集性
組成はさまざまですが、ハードコーティングは通常、製品の表面を硬化させるために使用されます。 それらは、窒化物(窒化チタン、TiN)、炭化物(炭化タングステン、WC)、または他のタイプ(ダイヤモンドライクカーボン、DLC)である可能性があります。 それらの機能は単純な硬化を超えており、腐食から保護したり、部品の摩耗を減らしたり、血液と接触している材料に血栓が形成されないようにするために使用されるものもあります。 それらは多くの異なった技術で多くの異なった基質に適用されます。
このノートでは、Rtecインデンテーション&スクラッチ試験機 SMT-5000を使用したハードテストのスクラッチ接着および凝集力について説明します。
ご質問はございますか
問題のあるスクラッチテスト
それらの機能性を考えると、ハードコーティングは固有の強度と堆積される基板への接着の両方について特徴付けられる必要があります。 例えば、コーティングの耐食性はコーティング表面に亀裂が発生するとすぐに低下します。 医療機器の場合、例えばインプラントへの耐摩耗性コーティングの接着は、コーティングの「チップ」が血流に入り患者の健康を脅かすことがないことを保証する必要があります。
しかし、接着は材料特性ではなく加えられた応力場に対するコーティング/基板システムの応答であるため定量化するのが難しい特性です。 スクラッチテストはコーティングを破壊しその基板から剥離する可能性のある応力を誘発するためによく使用されます。これによりコーティングの接着性をよりよく理解できます。 1回のテストで凝集力と接着力の両方の破損を研究できることは、コーティング製品を改善しようとしている研究者と産業エンジニアの両方にいくつかの利点をもたらします。
コーティング方法論 スクラッチテスト
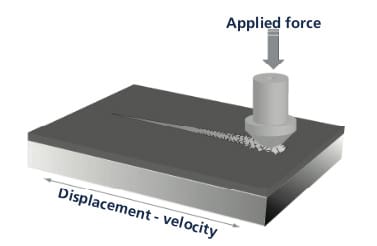
図1:スクラッチテストの原理
図1に示すように、既知の形状のダイヤモンドチップを対象のサンプルの表面上にドラッグするとスクラッチが作成されます。チップが表面に沿って移動するとチップにかかる通常の荷重が直線的に増加し接触が重大になります。 スクラッチに続いてスクラッチ全体の画像が撮影されさまざまな変形や故障が分析されます。
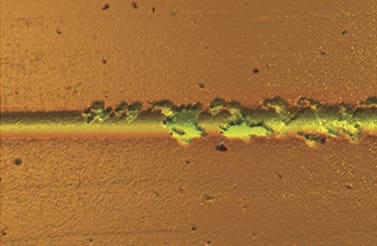
図2:スクラッチ障害の共焦点画像
障害が発生する通常の負荷は、クリティカル負荷、LCと呼ばれます。
臨界負荷は、イメージングまたはイメージングと信号の組み合わせ(アコースティックエミッションなど)のいずれかを使用して検出されます。
臨界負荷は、イメージングまたはイメージングと信号の組み合わせ(アコースティックエミッションなど)のいずれかを使用して検出されます。
コーティングの除去による破損を表す臨界荷重は、接着強度の定量的な代用です。 スクラッチテスト中に複数の信号を記録できるため、ユーザーは動作と特定の測定値を相互に関連付けることができます。
スクラッチ接着および凝集試験条件
インデンテーション&スクラッチ試験機(SMT-5000)を使用して、TiNと2つのDLCの3つのハードコーティングにスクラッチを作成しました。 テストパラメータは表1にまとめられています。
荷重方法 | 線形増加 |
スクラッチ長 | 2 mm |
初期荷重 | 0.1 N |
最終荷重 | 15 N |
スクラッチ速度 | 4 mm/min |
試験片(尖筆) | Rockwell φ100mm |
図3:機器のサンプル
スクラッチテストの結果
すべての場合において垂直力が増加するとコーティングは最初に凝集的に破損し、次に接着剤で図4に通常の引っかき荷重が15Nまで増加した場合の2つのサンプルの侵入深さと摩擦係数を示します。
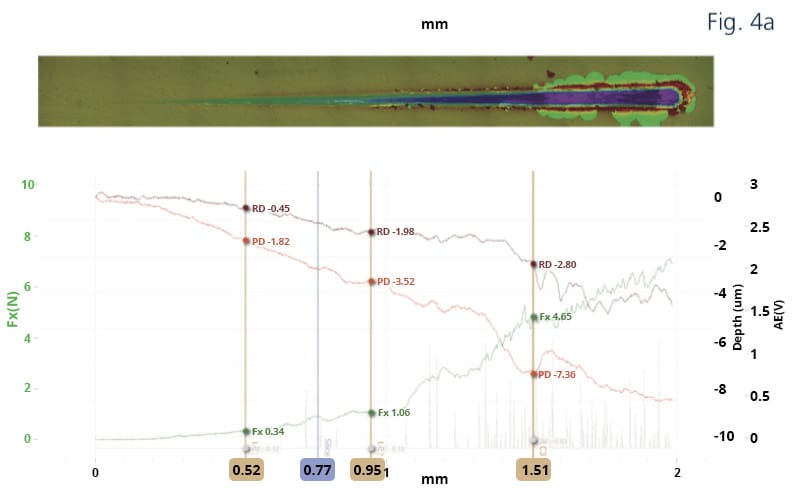
図4:DLC 2(左)とTiN(右)のサンプルの侵入深さ、引っかき荷重、摩擦係数、アコースティックエミッションと臨界荷重(垂直線)のプロット。
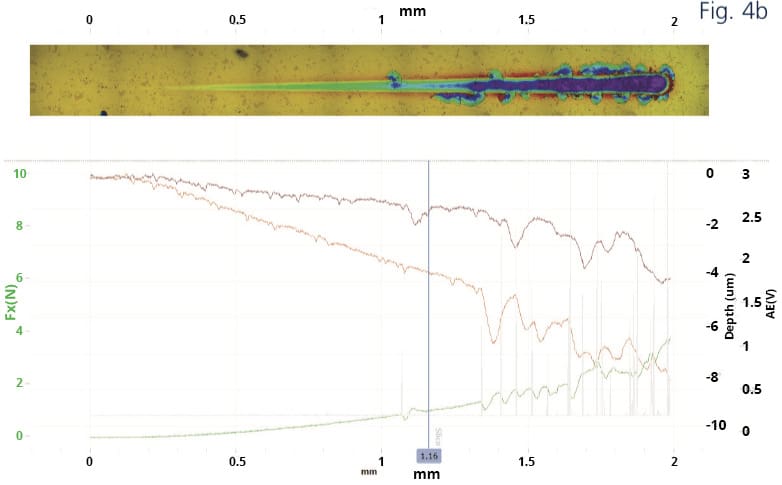
図4ab:侵入深さ、引っかき荷重、摩擦係数、アコースティックエミッションと臨界荷重(垂直線)のプロット
DLC 2(4a)およびTIN(4b)サンプルの場合
DLC 2(4a)およびTIN(4b)サンプルの場合
この場合、3つのタイプの障害が記録されます。
Lc1:コーティングの最初の亀裂
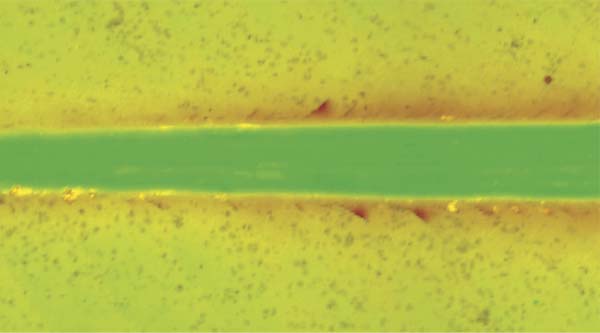
図5:DLC 2コーティング(Lc1)の最初の不良
Lc2:コーティングの最初のチッピング
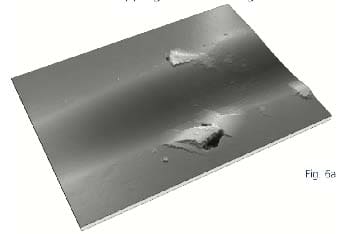
図6a:DLCコーティングの最初のチッピング(Lc2;接着剤)
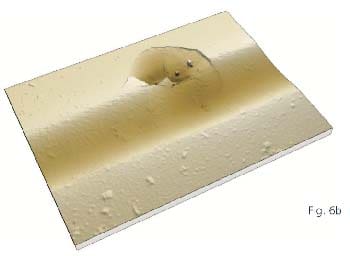
図6b:TiNコーティングの最初のチッピング(Lc2、凝集性)
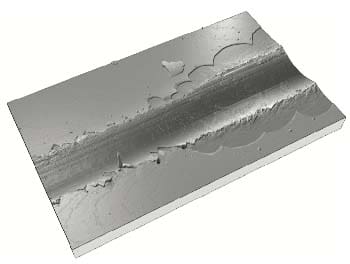
図7:DLCコーティング(Lc3)の完全な除去
Lc3:コーティングの完全な除去
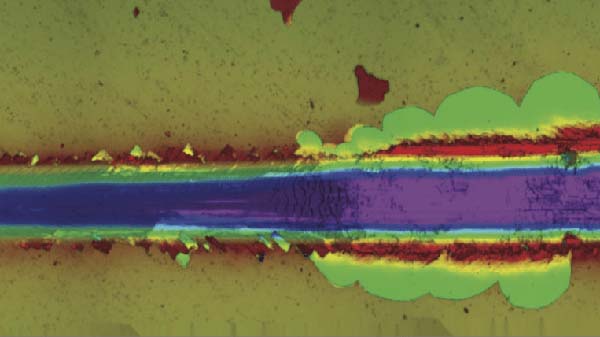
スクラッチ評価テストの概要と結論
図8:DLC 1およびTiNサンプルの浸透深度と残留深度は、サンプルの回収率を示しています
DLCサンプルの場合、摩擦係数とアコースティックエミッションの変化は最初の故障(Lc1)の優れた指標となり、共焦点画像ではLc2とLc3の詳細を提供します。 TiNサンプルでは、アコースティックエミッションは最初の2つの障害(Lc1とLc2)を検出するための優れた信号を提供し、明視野での光学的観察はLc3に必要な検出を提供します。 引っかき傷の侵入深さ(荷重下)とサンプルに残っている溝の残りの深さの比較は、引っかき傷の変形後のサンプルの回復に関する貴重な情報を提供します。
このプロットは、コーティング/基板システムの弾性回復を特徴づけます。 図9に示すように臨界負荷はサンプルの優れた比較を提供します。
Lc1はサンプル間で有意差を示しませんが、Lc2とLc3はDLCサンプルよりもTiNサンプルの優位性を示しています。 DLC 1(Lc2)の付着力は、3つのサンプルすべての中で最悪です。
結論
スクラッチテスト技術は、コーティングの挙動を区別するための貴重なツールです。 スクラッチテスト中に発生する応力は、最初にコーティングの強度に関する情報を提供しますが、上記のようにコーティングと基材の間の接着に関する情報も提供します。 共焦点および明視野イメージングによって提供される堅牢なイメージングに加えて、スクラッチテスト中に記録されたすべての信号を注意深く分析することで、コーティング/基板システムの動作を最も高度に理解できます。
国際規格
ASTM C 1624-05
“Standard test method for adhesion strength and mechanical failure modes of ceramic coatings by quantitative single point scratch testing.”
「定量的一点スクラッチ試験によるセラミックコーティングの接着強度と機械的破損モードの標準試験方法。」
“Standard test method for adhesion strength and mechanical failure modes of ceramic coatings by quantitative single point scratch testing.”
「定量的一点スクラッチ試験によるセラミックコーティングの接着強度と機械的破損モードの標準試験方法。」
3Dスクラッチ試験機にはさらに多くの機能がありますか
インデンテーション&スクラッチ試験機についてもっと知りたいですか。
用途の広いスクラッチテストが必要ですか
多機能トライボメーター、摩擦摩耗試験機 MFT-5000
もっと知りたいですか?
ご質問など、お問い合わせください。
おすすめ機種
インフォメーション
© Copyright 2021 Rtec-Instruments - All Rights Reserved