自動車用塗料のスクラッチテスト
ご質問はございますか
問題のあるスクラッチテスト
既存のクリアコートの高品質にもかかわらず、材料の性能を改善して寿命の間に自動車によって見られる機械的損傷に抵抗するための需要が高まっています。今日まで、相手先ブランド供給(OEM)は、CrockmeterやAmtek-Kistler洗車などの簡単なテスト方法を使用して、引っかき傷やその他の機械的負荷に対するクリアコートの耐性を評価しています。しかしクリアコートの品質が向上するにつれて、これらのテストでは標準偏差が大きく比較的主観的な結果が得られるため材料に加えられた改善を区別できません。
最近ではスクラッチテストにより、自動車のクリアコートに見られる実際の機械的損傷を再現しクリアコートの材料をわずかに改善するための優れた差別化要因を提供できることが示されています。自動車のクリアコートはさまざまな種類の損傷を受けます。
- 洗車ブラシは、比較的鋭くて小さな粒子で小さな引っかき傷を作ります。 これはしばしばmarと呼ばれます。
- 爪と木の枝はより大きなサイズの接触を示し、マイクロスクラッチとして特徴付けられるより深いスクラッチを生成します。 キーやショッピングカートは、大きくて深い傷を作る可能性があり、クリアコートが剥がれることがあります。
したがって、クリアコートの配合はマイクロスクラッチおよびマクロスクラッチ耐性とともに、製品の耐傷性(ナノスクラッチ)をテストする必要があります。 Rtec Instrumentsは、このタイプのスクラッチテストに完全に適合しており、単一のプラットフォームでナノスケールからマクロスケールまで高精度で交換可能なヘッドを提供する唯一の企業です。
スクラッチテストの方法論
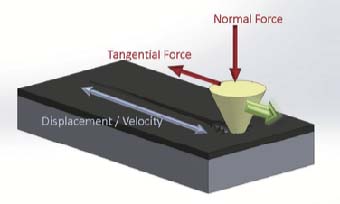
図2:スクラッチテストの原理
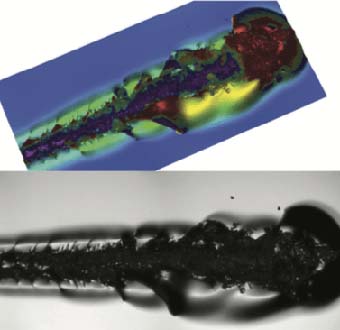
図3:スクラッチ障害の共焦点画像
スクラッチテスト条件
Mar レンジ | マイクロレンジ | マクロレンジ | |
---|---|---|---|
ダメージシミュレーション | 洗車、緩衝 | 釘、鍵、木の枝 | ショッピングカート、ベルトバックル、コートジッパー |
荷重 | 線形増加 | 線形増加 | 線形増加 |
スクラッチ長 | 2mm | 2mm | 2mm |
初期荷重 | 0 N | 0.1 N | 0.1 N |
最終荷重 | 0.5 N | 8 N | 20 N |
スクラッチ速度 | 4 mm/min | 4 mm/min | 4 mm/min |
チップ | Rockwell Φ2 µm | Rockwell Φ50 µm | Rockwell Φ200 µm |
自動車用塗装試験結果のスクラッチ試験
Mar テスト:
鋭いダイアモンド(2 µm)と小さな力(<1 N)を使用すると、たとえば洗車機のブラシによって引き起こされる損傷をシミュレートできます。 この場合、図3に示すように、1つのタイプの障害のみが観察されます(まとまりがあります)。
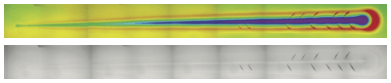
マイクロスクラッチ:
クリアコートの枝や爪によって引き起こされる引っかき傷をシミュレートするために、10〜20 Nの垂直抗力を持つより大きな半径の先端(50 µm)が使用されます。 この場合、図4に示すように、凝集と除去の両方が観察されます。
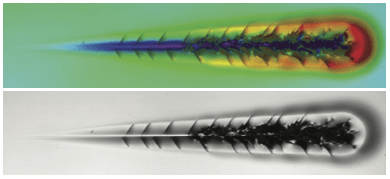
Figure 4: Confocal and bright field images of Micro scratch on automotive paint
マクロスクラッチ:
大きな先端半径(200 µm)と大きな法線力を使用して、キーで積極的に引っかいたり、ショッピングカートをこすったりしたときに、クリアコートが被る大きな引っかき傷を再現します。
これらの引っかき傷の場合、図5に示すように、クリアコートの除去は凝集破壊後比較的迅速に行われますが、ベースコートにさらに深い損傷を与えます。
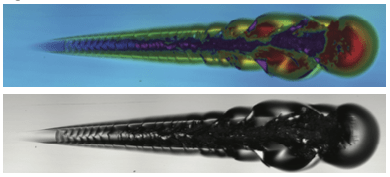
Figure 5: Confocal and bright field images of Macro scratch on automotive paints
Lc1:クリアコートの最初のひび割れ(粘着性)
Lc2:クリアコートの除去の最初の兆候
Lc3:クリアコートの完全な除去と下にあるベースコートの損傷
2つの異なるクリアコートを比較するために2つのペイントパネルがテストされました。 各力の範囲について、Lcでの臨界荷重と引っかき深さの結果を表2に示し、図12にプロットします。
サンプル 1 | Lc1 [N] | CD1 [µm] | Lc2 [N] | CD2 [µm] | Lc3 [N] | CD3 [µm] |
---|---|---|---|---|---|---|
Mar | 0.19 | 3.17 | ||||
マイクロ | 2.63 | 23.60 | 8.7 | 43.63 | ||
マクロ | 2.9 | 12.44 | 6.88 | 33.72 | 13.68 | 61.37 |
サンプル 2 | Lc1 [N] | CD1 [µm] | Lc2 [N] | CD2 [µm] | Lc3 [N] | CD3 [µm] |
---|---|---|---|---|---|---|
Mar | 0.28 | 2.48 | ||||
マイクロ | 1.84 | 25.02 | 3.53 | 33.80 | ||
マクロ | 2.45 | 16.35 | 7.67 | 33.02 | 15.75 | 61.56 |
結論
Tスクラッチテスト中に発生する応力は、最初にクリアコートの強度に関する情報、およびベースコートとその下のコーティングからのクリアコートの除去に対する耐性に関する情報を提供します。 共焦点および明視野イメージングによって提供される堅牢なイメージングに加えて、スクラッチテスト中に記録されたすべての信号を注意深く分析することで、さまざまなスケール(マー、ミクロ、マクロの損傷)での自動車塗装システムの動作を最も高度に理解できます。
国際規格
“Standard Test Method for Measuring Mechanistic Aspects of Scratch/Mar Behavior of Paint Coatings by Nano-scratching”「ナノスクラッチによる塗料コーティングのスクラッチ/マール挙動の機構的側面を測定するための標準試験方法」
ISO 1518
“Paints and varnishes – scratch test”「塗料とワニス-スクラッチテスト」
3Dスクラッチ試験機にはさらに多くの機能があります
用途の広いスクラッチテストが必要ですか
もっと知りたいですか?
ご質問など、お問い合わせください。
おすすめ機種
インフォメーション
© Copyright 2021 Rtec-Instruments - All Rights Reserved